Permian Construction: Working Smarter and Saving Money
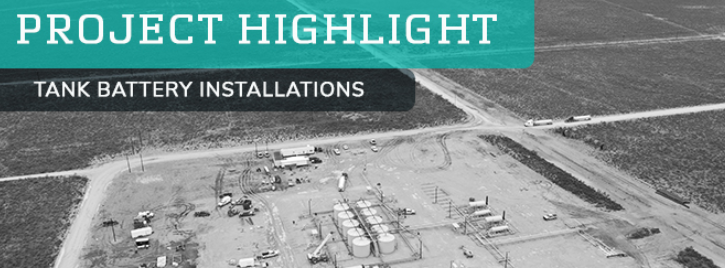
What's the difference between a good project and a great one? Improvement. What drives improvement? Relentless pursuit of better solutions. That sometimes means solving problems in counterintuitive ways or changing how you work. At Danos, the key to our success in the Permian has been the speed and pace of which we've been learning, improving and innovating. And we're not done yet.
To understand how far we’ve come, it helps to look back at where we’ve been. In 2018, Danos completed two projects for a Permian Basin client. These were greenfield tank battery installations, each situated about 50 miles south of Midland, among Danos’ first major construction projects in the area. The installation was completely turnkey, involving the company’s fabrication, project management, construction, automation, coatings and scaffolding services. Both of the 10,000-barrel processing and storage facilities were completed within the 95-day schedule required by the customer, but not without extraordinary effort. Danos was able to save time and money by performing 30% of the required field-welds in its Larose, Louisiana, fabrication shop, reducing labor costs even with additional transportation costs. Even so, the work required 24 hours a day, seven days a week scheduling in order to finish on time, adding to the project cost.
It wasn’t easy, but Danos got the job done. Meanwhile, the project leaders identified a new approach that they believed would dramatically improve similar projects. So they pitched the idea to the customer, who agreed to work with Danos to try it on a third installation project in the area.
Over the span of about three months in 2019, Danos personnel (including engineers) worked directly with the client to incorporate Danos' ideas for improving the facility design's constructability. By making these changes, Danos was able to perform a much higher portion of the welding and prefabrication work in Larose, reducing field costs for the client. For example, Danos added plant grid coordinates to all isometric drawings and reoriented the coordinate system, so it could be integrated seamlessly with the company's Total Station process.
With these changes implemented, Danos was able to complete the third tank battery facility in 85 days, without the need for 24/7 operations. But most importantly, Danos was able to handle 96% of field welds in-shop, saving the client substantial money and time. Moreover, the amount and type of man hours required also changed. On the first two facilities, approximately 40,000 man hours were needed for construction and fabrication (most of which were on-site labor, twice the rate of in-shop labor). But for the third project, the overall man-hour total was reduced to about 27,000, with only half of those hours needed on-site. This cut the overall time-in-field by half! By improving efficiency and moving more work into the shop, Danos saved the client $1.58 million, or about 35% off the project total.
According to the client’s Permian construction manager, the project “was executed perfectly. We’d be happy if all our projects went this well. From the quality to the safety and the labor saved, it was an all around success.”
While a happy client is always the goal, Danos felt there was room for even more improvement. Since completing these projects, the company has implemented a new method for handling on-site measurements which has not only decreased the time required by 75% and labor needed (six workers down to two), it has also improved measurement accuracy.
At Danos, we pride ourselves on overcoming any challenge and constantly striving for improvement. Learn more about how we are solving big challenges for our customers and our communities at www.danos.com.Whereas manual measurement practices generally have about 1/4 inch margin of error, Danos’ use of three-dimensional survey equipment brought the margin of error down to only 1/16 of an inch. And the proof was in the result: all pre-measured, prefabricated components were installed as planned with no need to rework or adjust on site, and the weld-repair rate was only .08%. Since these successes, Danos has won several more projects in the area, providing more opportunities to refine processes in order to achieve even better results. At Danos, we’re never satisfied with just a “job well done.”